歐標(biāo)托盤的生產(chǎn)周期能否縮短取決于企業(yè)生產(chǎn)模式與技術(shù)應(yīng)用的優(yōu)化水平。通過系統(tǒng)性改進(jìn),生產(chǎn)周期可壓縮30%-50%,主要從以下維度實現(xiàn):
1. 工藝鏈重構(gòu)
采用并行生產(chǎn)模式替代傳統(tǒng)線性流程,實現(xiàn)原料預(yù)處理、板材切割、組件加工等工序同步推進(jìn)。德國某制造商通過模塊化分組作業(yè),將生產(chǎn)周期從72小時壓縮至42小時。
2. 智能設(shè)備集成
引入五軸數(shù)控加工中心可實現(xiàn)托盤組件誤差±0.3mm的精密加工,較傳統(tǒng)設(shè)備效率提升4倍。自動釘合系統(tǒng)裝配速度達(dá)120片/小時,較人工操作效率提高300%。
3. 供應(yīng)鏈協(xié)同優(yōu)化
建立JIT原料供應(yīng)體系,將木材庫存周期從15天縮短至3天。采用RFID原料系統(tǒng),使各環(huán)節(jié)物料流轉(zhuǎn)效率提升40%。
4. 數(shù)字化生產(chǎn)管理
部署MES系統(tǒng)后,某西班牙企業(yè)設(shè)備利用率從65%提升至88%,訂單交付周期縮短37%。通過大數(shù)據(jù)分析設(shè)備OEE,故障停機(jī)時間減少60%。
5. 標(biāo)準(zhǔn)化質(zhì)量管控
實施在線視覺檢測系統(tǒng),檢測效率達(dá)每分鐘15個托盤,較人工檢測提速5倍,同時將次品率控制在0.5%以下,避免返工損耗。
值得注意的是,生產(chǎn)周期壓縮需平衡質(zhì)量與成本。建議企業(yè)分階段實施改造,初期可重點優(yōu)化切割與裝配環(huán)節(jié),中期引入自動化設(shè)備,后期構(gòu)建數(shù)字化生產(chǎn)體系。通過系統(tǒng)化改進(jìn),完全可實現(xiàn)周轉(zhuǎn)型生產(chǎn)向按需制造的轉(zhuǎn)型升級。
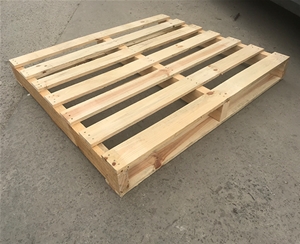